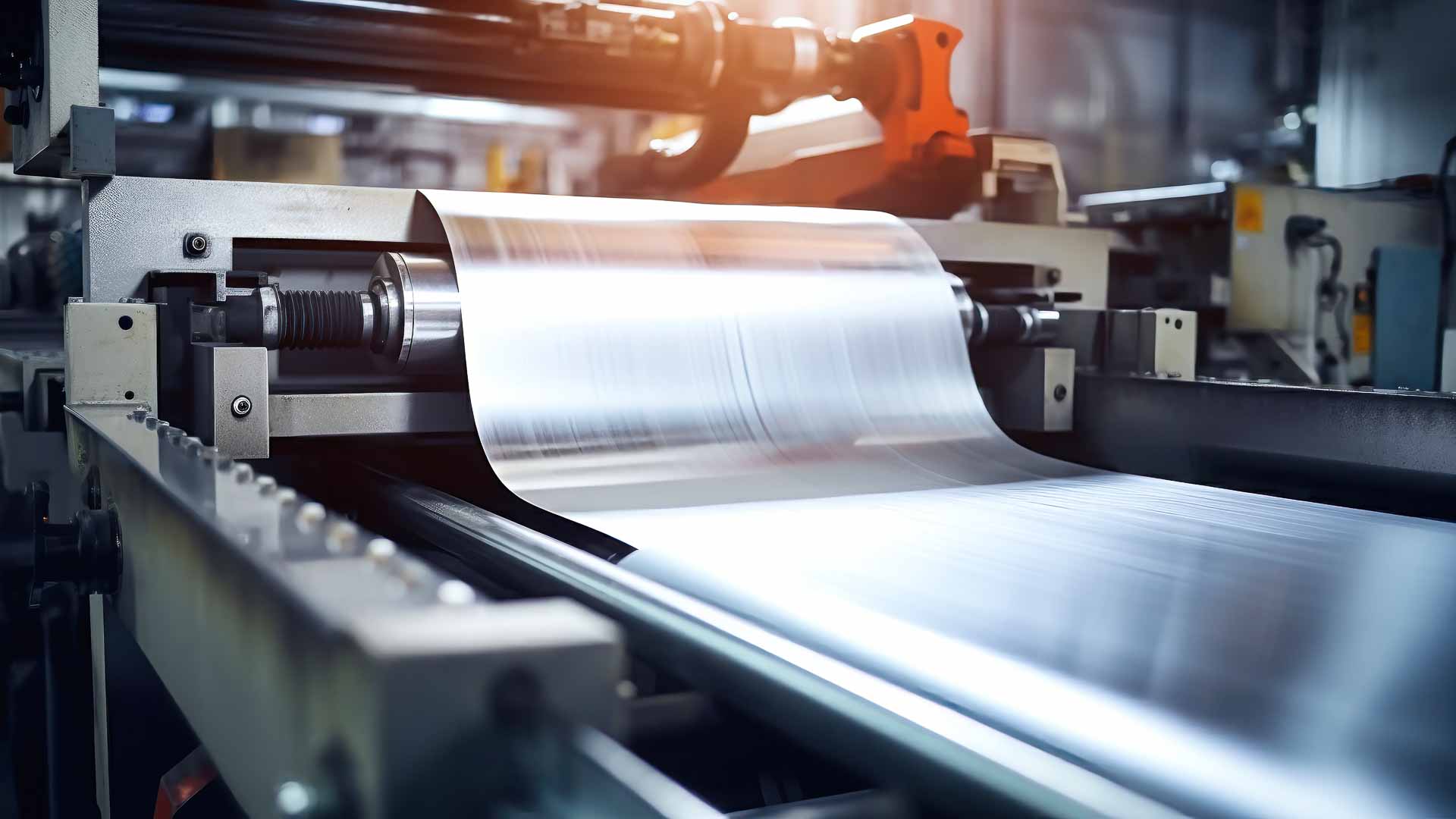
Einwandfreie Oberflächenqualitäten für ein perfektes Endprodukt
Mit den zunehmenden Investitionen vieler Länder in die Elektromobilität werden Batterien schnell zu einem zentralen Bestandteil für die Mobilität der Zukunft und sorgen für einen Boom bei der Herstellung von Lithium-Ionen und anderen Batterien.
Batterien bestehen heute meistens aus zwei Metallfolien, welche durch ein Elektrolyt miteinander verbunden sind. Das Elektrolyt wird durch Kalandrieren als Suspension (engl. Slurry) oder neuerdings auch direkt als Pulver im Trockenbeschichtungsverfahren auf die Folie aufgebracht. Beim Walzen von Batteriefolie sind einwandfreie Oberflächen entscheidend.
Denn bereits kleinste Kratzer oder Beschädigungen der Trägerfolie können zu schwerwiegenden Fehlern in der fertigen Zelle führen, die letztlich zu teurem Ausschuss führen. Herkules Maschinen punkten hier vor allem durch ihre Mess- und Inspektionstechnologie zur frühzeitigen Erkennung von Defekten im Walzeninneren und auf der Oberfläche, aber auch durch ein stabiles und robustes Design − das weiß auch Ralf Klews, Senior Sales Manager der Firma Herkules und seit vielen Jahren tätig in der Branche.
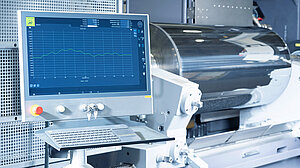
Welche Ansprüche haben unsere Kunden an das Endprodukt?
Klews: Im Bereich der Batteriefolienproduktion gibt es unterschiedliche Anforderungen an die Walzenoberflächen, die erreicht werden müssen. Dabei hängen diese von verschiedenen Faktoren ab, z. B. von der Art der Batteriefolie, dem Beschichtungsverfahren und den gewünschten Eigenschaften der Folie. Um eine Verbindung zwischen Trägerfolie und Elektrodenmaterial ohne Delaminierung zu garantieren ist eine sehr homogene Oberfläche auf der gesamten Folienbreite notwendig. Das betrifft unter anderem die Topographie, also die Rauheit, die Struktur der Oberfläche und die Elastizität sowie die Temperaturbeständigkeit. Zudem muss die Walzenoberfläche auch unterschiedlichen chemischen Einflüssen standhalten, beispielsweise einer bestimmten Korrosionsbeständigkeit gegenüber den Beschichtungsverfahren, die angewendet werden.
Eine einwandfreie Oberfläche bedeutet also ein besseres Produkt: Mit welchen Mess- und Inspektionstechnologien lässt sich die Homogenität der Oberfläche sicherstellen?
Klews: Unsere feinfühlige Mess- und Steuerungstechnik hält den Strom, also den Druck der Schleifscheibe gegen die Walze, während des Finishings in einem extrem kleinen Fenster von +/-0,3 % konstant – so wird eine extrem homogene Oberfläche hergestellt. Mit dem Roughness Scattered Light Detection System (RSLD) wird der komplette Walzenballen mit Hilfe von Streulicht auf Rauheit geprüft. Auch unser Roll Surface Inspection System (RSIS-Messsystem), welches mittels reflektiertem Laserstrahl mögliche Oberflächendefekte zuverlässig erkennt und mit einer Schwellenanalyse die Oberflächenqualität der Walze bestimmt, ist unabdingbar für perfekte Homogenität. Defekte werden so effizient im Vorfeld erkannt und unnötige Walzenwechsel auf ein Minimum reduziert, um die Produktivität des Walzwerks zu erhöhen.
Welche Herausforderungen ergeben sich beim Beschichten von Batteriefolien?
Klews: Die fertig beschichtete Folie sollte so dünn wie möglich sein. So ergeben sich höhere Kapazitäten in der Batterie. Gleichzeitig muss sichergestellt sein, dass die Folien zueinander ausreichend isoliert sind – ansonsten kommt es zu Spannungsspitzen, die letztendlich zum Brandrisiko führen. Auch hier zeigt sich wieder, wie wichtig die homogene Rauheit der Oberfläche ist.
Wie erreichen unsere Maschinen diese geforderten Qualitätsstandards?
Klews: Unsere Maschinen sind, aufgrund unserer Mess- und Steuerungstechnik, genau auf die hohen Anforderungen in der Herstellung von Batteriefolien spezialisiert. Beispielsweise hat sich unser indischer Kunde Hindalco Industries Limited, das Metall-Flaggschiff der Aditya Birla Group, für seinen Standort in Mumbai zum Kauf einer WS 450 L × 4500 CNC Monolith™ entschieden, weil sie unter anderem Aluminium-Flachwalzprodukte, -folien und Aluminiumverpackungen einwandfrei produzieren kann.Mit unserem Produkt ist unser Kunde Hindalco in der Lage, die nächste Stufe der hochfeinen und absolut makellosen Batteriefolienproduktion zu definieren und zu erreichen. Herkules Steuerungs- und Messtechnik ist die erste Wahl bei der Herstellung von Batteriefolien. Mit Hunderten von Maschinen im Bereich der Folienproduktion und mehr als 30 Maschinen allein für die Batteriefolienproduktion ist Herkules die beste Wahl für diese anspruchsvollen Anforderungen. Das Ergebnis spricht für sich: Größte Effizienz und hochpräzise geschliffene Walzen bei gleichzeitig hochkomfortabler und intuitiver Bedienung über das Touchpanel.
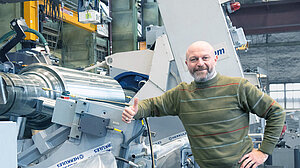
Ihre persönliche Meinung: Wie wird sich die Branche entwickeln und welche Herausforderungen werden sich zukünftig ergeben?
Klews: Meiner Meinung nach sind die Weichen in eine batterieelektrische Zukunft gestellt. Ein Beispiel: In Chinawurde gerade das erste batterieelektrische Containerschiff zu Wasser gelassen – 42 Standardcontainer sind mit Batterien bestückt – diese werden im Hafen gegen frisch geladenen (Batterie-) Container getauscht. Wenn sich das durchsetzt, werden in den nächsten Jahrzehnten immense Kapazitäten zur Batterieproduktion geschaffen werden müssen. Am anderen Ende der Wertschöpfungskette, dem Recycling der Batterien, tut sich ebenfalls einiges. Die zur SMS gehörende Firma Primobius wirbt damit, 96 % der wertvollen Rohstoffe zur Wiederverwendung zu extrahieren. In Kooperation mit Mercedes Benz entsteht gerade eine Pilotanlage, um dahingehend weltweit neue Standards zu setzen. Es bleibt also spannend und ich bin dankbar, dass Herkules – und auch ich persönlich – unseren Beitrag zu dieser Transformation leisten können.